鈦合金是“輕質、高強度、耐熱”材料的典型代表,在工程領域應用廣泛。 其中,最具代表性的應用領域是航空航天領域,如用于制造飛機發動機的風扇葉片、壓縮機的葉片、葉輪、飛機外殼和飛機機翼等[1-4]。 然而,航空航天領域對零件加工精度及其表面質量的高要求,決定了人們需要采用更高精度的加工方法來加工鈦合金材料[5-7]。
由于鈦合金存在高彈性、高粘性、高硬度和低導熱性等特性, 在傳統機械加工中會出現刀具磨損、加工表面易燒傷、加工過程切削力大等一系列問題,不利于鈦合金的高效精密加工[8-10]。旋轉超聲加工在難加工材料領域具有顯著優勢,可在傳統機械加工基礎上通過對刀具頭施加超聲頻率的振動,實現加工過程中的斷續接觸,降低加工時的切削力和減小加工時產生的切削熱,以提高加工效果,進而實現對難加工材料的高精度加工[11-13]。
在金屬加工領域,旋轉超聲加工技術已體現出優勢。例如,有研究人員采用旋轉超聲加工技術加工鈦合金,提高了鈦合金的加工效果[4],或降低了加工過程中的切削力并提高加工后的鈦合金表面質量[15-17。但是對于旋轉超聲加工后的工件表面粗糙度值是增大或減小的問題,存在不同研究結果[18-19]。
為此,研究者需進一步探究超聲加工對表面粗糙度的影響機制。
此外,現有超聲輔助銑削鈦合金研究中所用超聲裝置通常不具有頻率跟蹤或振幅穩定控制裝置,對加工過程中振幅穩定性影響加工效果的方面缺乏探究,限制了超聲加工裝置在鈦合金銑削中的進一步應用。本文分別開展了側面銑削和端面銑削的驗證實驗,研究了不同形式旋轉超聲加工對加工效果的影響,對比探究了普通加工、無調控超聲和有振幅穩定控制的超聲三種情況對加工中的切削力、加工后的工件表面質量及微觀結構的影響。
1、實驗方案
1.1實驗原理
旋轉超聲加工是一種在常規旋轉銑削基礎上,通過對刀具頭施加超聲頻率振動來提高加工性能的技術。鈦合金旋轉超聲銑削加工原理見圖1。
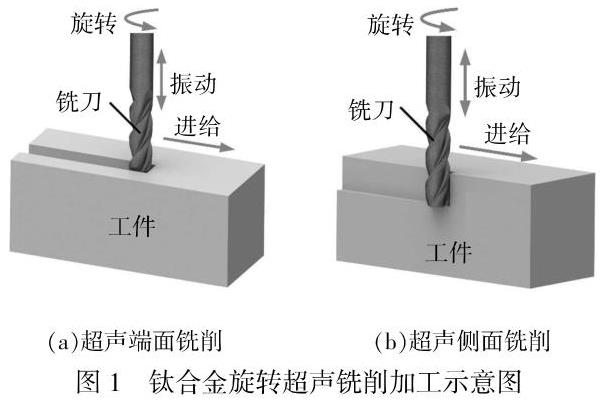
在超聲加工中,刀具運動為旋轉運動、進給運動與超聲振動的疊加,刀具在實際加工中的切削速度增加,加工表面被刀具反復犁削,提高了加工效果;同時,加工過程中的超聲振動作用會使刀具和工件之間產生間歇性的接觸效應,減少了接觸時間以及加工過程中的切削力和切削熱;此外,刀具的振動使切削液更易流人刀具和工件接觸的表面,能充分發揮切削液的冷卻和潤滑作用。因此,使用超聲銑削加工鈦合金可降低切削力和銑削熱,并改變工件的表面微觀形貌。
1.2實驗裝備與設備
基于自主開發的超磁致伸縮旋轉超聲加工系統,本研究分別開展側面銑削和端面銑削實驗。實驗時,將該超聲加工系統安裝在VMCL-1100型三軸數控銑床上,并采用直徑為6mm、長度為50mm的銑刀來研究相關工藝特性。實驗平臺與旋轉超聲加工系統見圖2。
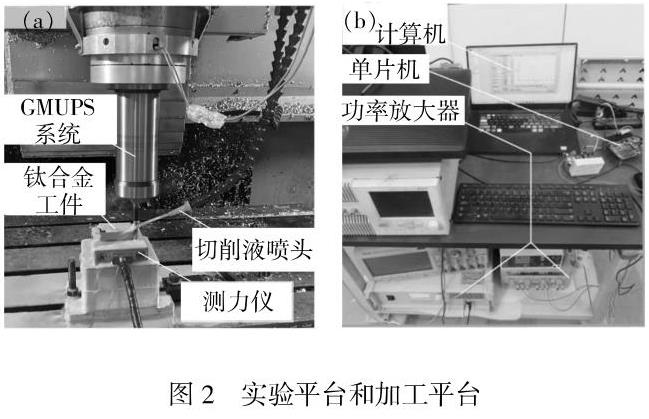
實驗采用ST210-S4標準銑刀,該刀具在側面銑削時的推薦切削速度不大于60m/min,在端面銑削時的推薦切削速度不大于40 m/min,并在加工時通過切削液進行冷卻;采用尺寸為80mmx40mmx15mm的長方體鈦合金為工件,并將該工件以螺栓固定的方式安裝于Kistler9256C2測力儀上,通過測力儀測量其加工過程中的切削力;實驗完成后,使用馬爾手持式表面粗糙度測量儀對工件表面粗糙度進行測量,并統計出加工過程穩定后的工件表面粗糙度;之后,再使用光學顯微鏡分別觀測加工穩定過程中和加工完成后的工件表面微觀形貌。觀測時,將顯微鏡放大至400倍,同時使用RX-100軟件讀取觀測到的圖像。
由于本研究聚焦于驗證超聲輔助銑削對鈦合金加工的影響和有效性,而非探究各切削參數對鈦合金銑削加工效果的影響,選用正交實驗方法分別開展側面銑削和端面銑削實驗,對比了普通加工、無調控超聲和有振幅穩定控制超聲的加工區別。在側面銑削和端面銑削正交實驗中,有超聲輔助時的空載振幅均為6μm,同時均探究了相同切削參數條件下不同超聲振幅對加工質量的影響。
側面銑削正交實驗的工藝參數是:主軸轉速為2500~3500 r/min、進給速度為200~300 mm/min、切削速度為47.1~65.9m/min、切削深度為20~80μm。采用表1所示9組側面銑削正交實驗工藝參數開展無超聲的普通加工, 另有 18 組實驗采用相同實驗參數,分別開展無調控超聲加工及有振幅穩定控制的超聲加工。 對于相同切削參數下不同超聲振幅影響的實驗, 選用的主軸轉速為 3 000 r/min、進給速度為 300 mm/min、切削深度為 50μm,以及振幅(銑刀上的)分別為 2、4、6、8、10、12μm。
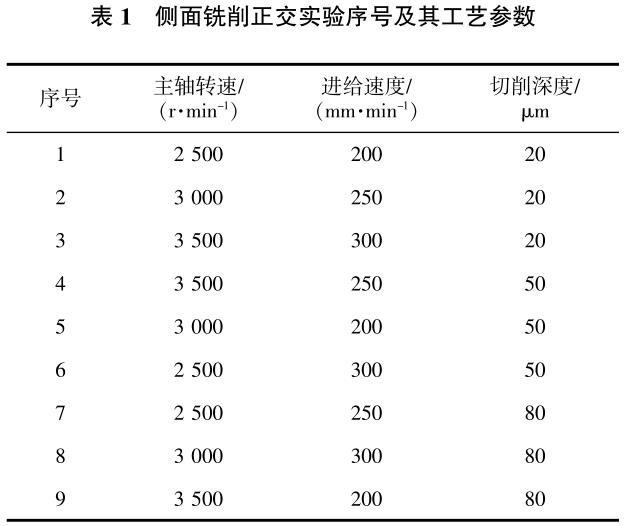
端面銑削正交實驗的工藝參數是:主軸轉速為1 500~2 500 r/min、 進給速度為 150~250 mm/min、切削速度為 28.3~47.1 m/min、 切削深度為 20~80μm。采用表 2 所示 9 組端面銑削正交實驗工藝參數開展無超聲的普通加工, 另有 18 組實驗采用相同工藝參數,分別開展無調控超聲加工及有振幅穩定控制的超聲加工。 對于相同切削參數下不同超聲振幅的影響實驗, 選用的主軸轉速為 2 000 r/min、進給速度為 200 mm/min、切削深度為 50 μm,以及振幅(銑刀上的)分別為 2、4、6、8、10、12 μm。 需要注意的是,在端面銑削正交實驗過程中設置的銑削深度為機床控制的切削深度。
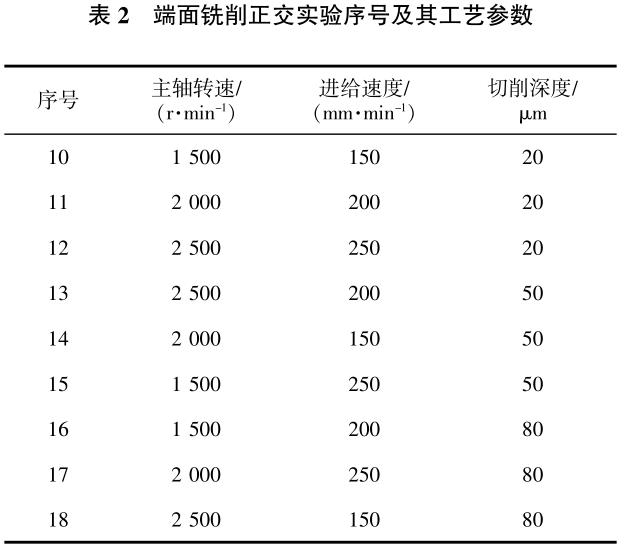
2、實驗結果及討論
2.1對切削力的影響
在側面銑削和端面銑削過程中,采用振幅穩定控制可實現最小的切削力。 對銑削加工實驗的結果進行分析,經測量各實驗組得到的加工穩定過程中的切削力見圖 3。 從側面銑削和端面銑削的實驗結果均可看到,普通加工時的切削力最大,有振幅穩定控制時能實現最小切削力,從而驗證了超聲加工能降低切削力。 需要注意的是,在端面銑削過程中,超聲加工減少切削力和超聲加工增加切削深度二者會共同作用,對于無振幅調控的超聲加工系統而言,由于系統的諧振頻率偏移,此時振幅降低,加工中切削深度的增加不穩定,即加工實際切削深度不穩定會影響系統加工精度, 尤其是當切深較小時,該影響顯著,從而阻礙了超聲加工在精密制造領域的進一步應用。 而具有振幅穩定控制的超聲加工系統,由于可穩定控制振幅,提高了加工過程中的切削深度控制精度,進而提高加工精度,實現了更精密的加工。
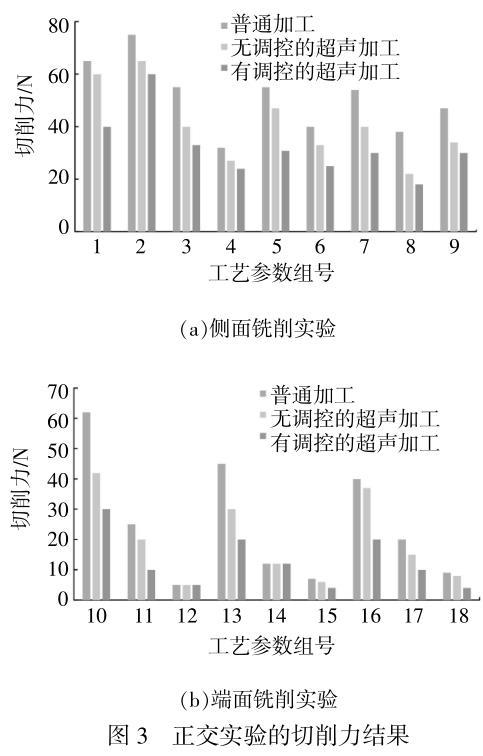
增大超聲振幅,可降低切削力。 采用不同超聲振幅在不同工況條件下得到的切削力結果見圖 4。可見,在側面銑削與端面銑削加工中,更大的超聲振幅帶來更小的切削力,這與超聲加工能提高切削速度、改善切削液的流入效果等有關。
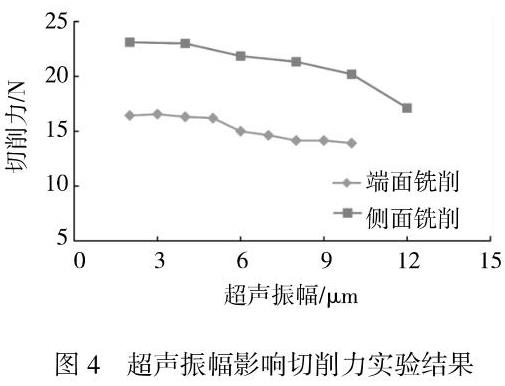
2.2對表面粗糙度的影響
測量的工件表面粗糙度結果如圖5所示,超聲在側面銑削與端面銑削加工中對工件表面粗糙度的影響不同。在側面銑削加工時,超聲加工可減小工件表面粗糙度值,顯著提高表面質量;有振幅穩定控制的超聲加工,也對減小表面粗糙度起到促進作用。在端面銑削時,除序號10對應的實驗組之外,其他實驗組通過超聲輔助增大了加工后的工件表面粗糙度值,有振幅穩定控制的超聲加工對此起到進一步增大的作用。產生該現象的原因在于,側面銑削對刀具和工件的剛性要求較高,但本研究所用刀柄的變幅桿懸長較長,在側面銑削時易發生顫振,導致普通加工的工件表面質量較差,而采用旋轉超聲加工后,刀具在加工時的切削力因超聲振動作用而減小,使顫振減少,從而提高了表面質量;在端面銑削時,刀具的受力情況發生變化,刀具不易顫振,使普通機械加工的工件表面質量得到大幅提高。在序號10對應的實驗中,加工過程的切削力較大(圖4),因此更易發生顫振等現象,此時使用超聲加工可減小切削力從而降低振動,也減小了加工后的工件表面粗糙度值。此時使用超聲振動,雖然仍可降低切削力,但是并不能起到減小顫振的效果,同時超聲振動會促使產生新的表面微織構,從而增大加工后的工件表面粗糙度值。
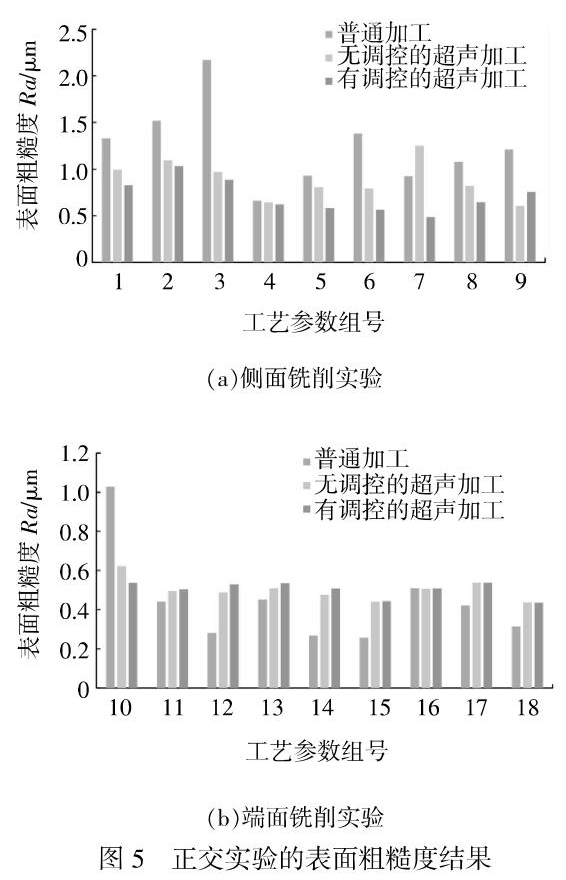
在側面銑削時,提高超聲振幅可減小工件表面粗糙度值;在端面銑削時,提高超聲振幅會增加工件表面粗糙度值。不同超聲振幅在端面銑削與側面銑削中影響表面質量的結果見圖6。可看到,在側面銑削時,較大的超聲振幅會帶來更小的表面粗糙度值,這與較大的振幅可更好地降低切削力、抑制加工過程中的振動有關;在端面銑削時,較大的超聲振幅會導致更大的表面粗糙度值,究其原因是更大的超聲振幅會導致形成尺寸更大的表面微結構,對加工后的工件表面粗糙度產生影響。
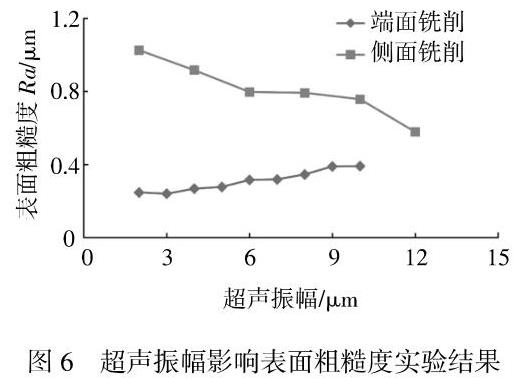
2.3對表面微觀形貌的影響
分別觀測普通機械加工、無調控旋轉超聲加工以及有振幅穩定控制的旋轉超聲加工的工件表面微觀形貌,結果見圖7和圖8。可見,在側面銑削的情況下,普通機械加工的工件表面會產生明顯振紋且出現了一定面積的燒傷;采用超聲輔助加工后,工件的表面振紋有所減少且加工出的微結構更加均勻、工件表面燒傷有所減少;采用振幅穩定控制的超聲加工后,工件的表面振紋與燒傷進一步改善,表面也產生了均勻的微結構。還可見,在端面銑削情況下,普通機械加工的工件表面存在明顯劃痕;在無調控的超聲加工后,工件表面出現微結構且不再存在刀具銑削后的劃痕;在采用振幅穩定控制的超聲加工之后,工件表面微結構的均勻性進一步提高。
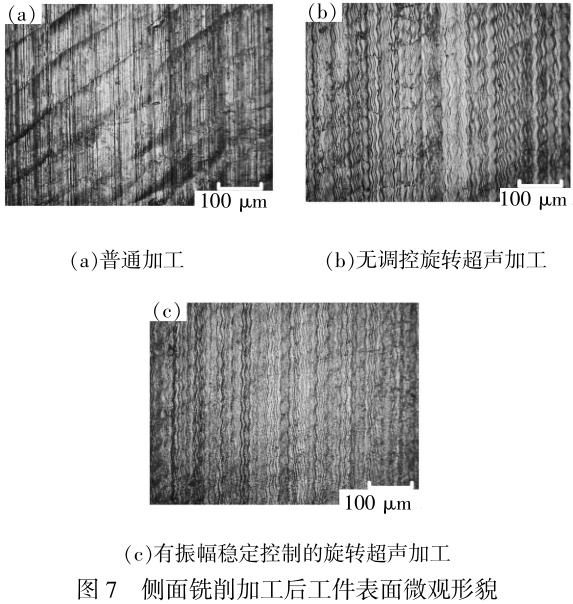
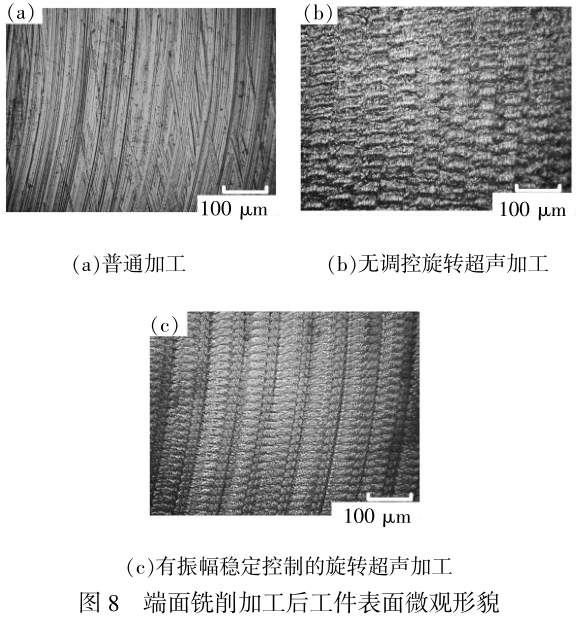
根據上述實驗和分析,在側面銑削和端面銑削過程中,較大的超聲振幅可降低加工過程中的切削力;在銑削過程中,在剛度較低的加工條件下,采用超聲加工可減小表面粗糙度值、提高加工后的表面質量,在剛度較高的加工條件下,超聲加工會導致表面粗糙度值增大,同時會減小加工過程中的振紋與燒傷,提高加工后表面的均勻性。
3、結論
本文研究了使用超聲輔助銑削工藝加工鈦合金的有效性,分別在側面銑削,端面銑削的條件下開展正交實驗,探究了超聲加工對加工過程中的切削力,加工后的表面質量與微觀形貌的影響,同時探究了超聲振幅的影響,得到以下結論:
(1)在側面銑削及端面銑削過程中,在不同的進給速度、主軸轉速和切削深度條件下,采用超聲加工可降低加工中的切削力,同時采用更大的超聲振幅可實現更小的切削力,而采用振幅穩定的超聲加工可增大加工過程中的實際超聲振幅,從而獲得最小切削力。
(2)側面銑削及端面銑削過程中,在不同的進給速度、 主軸轉速和切削深度條件下采用超聲加工,會使工件表面產生較為均勻的微結構并改變工件的表面粗糙度。 在側面銑削時,超聲加工可減少工件振動,從而降低表面粗糙度值,并且大的超聲振幅會帶來更好的表面質量,而采用穩定振幅超聲加工得到的表面粗糙度值最小。 端面銑削時不易發生顫振現象,并且更大的超聲振幅會帶來尺寸更加明顯的表面微結構,提高工件表面粗糙度值。
(3)相較于傳統方法,超聲輔助銑削可在保持加工質量的前提下提高切削速度和切削深度,即在相同加工質量標準下提高了加工效率。
參考文獻:
[1]AGRAWAL C,WADHWA J,PITRODA A,et al.Comprehensive analysis of tool wear,tool life,surface roughness,costing and carbon emissions in turning Ti-6Al-4V titanium alloy:cryogenic versus wet machining[J].Tribology International,2021,153:106597.
[2]HOURMAND M,SARHAN A A D,SAYUTI M,et al. A comprehensive review on machining of titanium alloys[J].Arabian Journal for Science and Engineering,2021,46:7087-7123.
[3]SHOKRANI A,Al-SAMARRAI I,NEWMAN S T. Hybrid cryogenic MQL for improving tool life in machining of Ti-6Al -4V titanium alloy [J]. Journal of Manufacturing Processes,2019,43:229-243.
[4]丁文鋒,奚欣欣,占京華,等. 航空發動機鈦材料磨削技術研究現狀及展望 [J]. 航空學報,2019,40(6):6-41.
[5]PEREIRA M F,ABRAO B S,ABRAO A S,et al. Influence of grinding wheel conditioning on the grindability of Ti -6Al -4V alloy [J]. The International Journal of Advanced Manufacturing Technology, 2023,125(3-4):1531-1542.
[6]SETTI D,YADAV N K,GHOSH S. Grindability improvement of Ti -6Al -4V using cryogenic cooling [J]. Proceedings of the Institution of Mechanical Engineers,Part B:Journal of Engineering Manufacture,2014,228(9):1131-1137.
[7]CUI X,LI C,ZHANG Y,et al. Grindability of titanium alloy using cryogenic nanolubricant minimum quantity lubrication [J].Journal of Manufacturing Processes,2022,80:273-286.
[8]劉世鋒,宋璽,薛彤,等. 鈦合金及鈦基復合材料在航空航天的應用和發展[J]. 航空材料學報,2020,40(3):77-94.
[9] LIU J J,JIANG X G,HAN X,et al. Effects of rotary ultrasonic elliptical machining for side milling on the surface integrity of Ti -6Al -4V [J]. The International Journal of Advanced Manufacturing Technology,2019,101(5/8):1451-1465.
[10]劉佳佳,姜興剛,高澤,等.高速旋轉超聲橢圓振動側面銑削削振幅對鈦合金表面完整性影響的研究[].機械工程學報,2019,55(11):215-223.
[11] WANG J J,ZHANG C L,FENG P F,et al. A model for prediction of subsurface damage in rotary ultrasonic face milling of optical K9 glass [J]. International Journal of Advanced Manufacturing Technology,2016,83 (1):347-355.
[12] CONG W L,PEI Z J,SUN X,et al. Rotary ultrasonic machining of CFRP:a mechanistic predictive model for cutting force[JJ. Ultrasonics, 2014,54(2) : 663-675.
[13] GONG H,FANG F Z,HU X T. Kinematic view of tool life in rotary ultrasonic side milling of hard and brttlematerials [J]. International Journal of Machine Tools and Manufacture,2010,50(3) :303-307.
[14] NIK M G,MOVAHHEDY M R,AKBARI J. Ultrasonic-assisted grinding of Ti6Al4V alloy [J]. Procedia CIRP,2012,1(1):353-358.
[15]張俊杰,劉英想,胡王杰,等.TC4鈦合金縱彎超聲振動銑削裝置及其加工性能研究[J].航空制造技術,2022,65(8) : 14-21.
[16]趙波,李鵬濤,張存鷹,等.超聲振動方向對TC4鈦合金銑削特性的影響[J].航空學報,2020,41(2):39-49.
[17]倪陳兵,朱立達,寧晉生,等.超聲振動輔助銑削鈦合金銑削力信號及切屑特征研究[J]機械工程學報,2019,55(7):207-216.
[18]韓雄,孫哲飛,耿大喜,等.高速超聲振動銑削鈦合金實驗研究[J].北京航空航天大學學報,2023,49(7):1707-1714.
[19]魏學濤.鈦合金超聲振動輔助銑削過程研究[D].哈爾濱:哈爾濱理工大學,2021
相關鏈接